As a green technology pioneer, INNIO Group has long focused on sustainability – with its technology and services as well as its own environmental footprint. Recently, a successful project aimed at cutting weekend energy use at its headquarters and advanced manufacturing facility in Jenbach, Austria, was recognized in a report published as part of the Energy Efficient End-Use Equipment (4E) Electric Motor Systems Platform (EMSA) program.
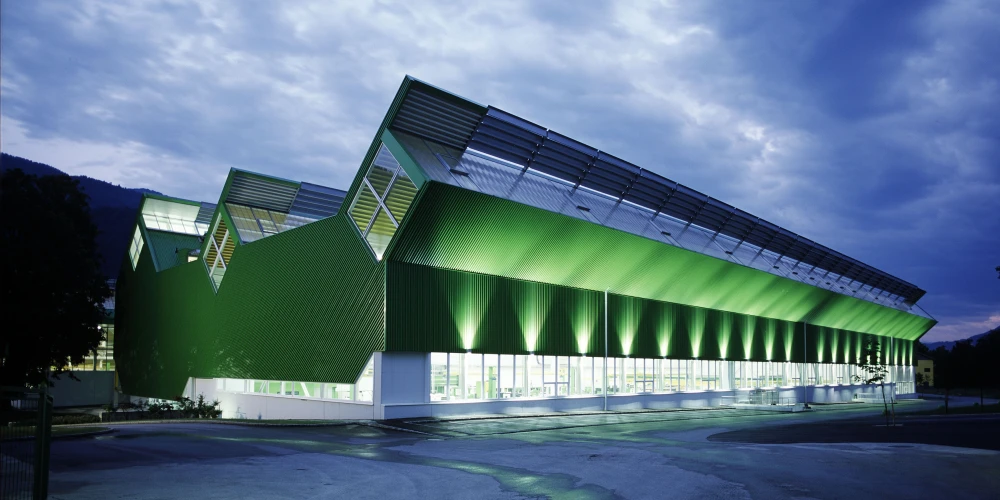
INNIO Group initiated the “energy shutdown over the weekend” project to enhance efficiency and reduce the environmental footprint of operations at its headquarters facility. Using Industry 4.0’s comprehensive energy management system, a project team conducted a thorough review of energy consumption within the advanced manufacturing facility with the goal of identifying opportunities to improve economic efficiency. The analyses revealed that minor modifications during weekends could yield significant efficiency gains and cost savings.
Pilot project implementation
Ongoing benefits
Building on the pilot project, INNIO Group has enhanced the transparency of its weekend operations with a new weekly report that clearly shows if the defined energy demand thresholds have been met. The report details the measured electrical energy and compressed air demand, as well as the associated CO2 emissions during non-operating weekend hours.
Experienced employees analyze the project data to pinpoint the main energy consumers and detect outliers in similar production machines, enabling the prompt identification of inefficiencies and the implementation of targeted solutions. Not only does this approach save energy, but it also helps boost the overall reliability and cost-efficiency of INNIO Group’s operations by enhancing equipment life-cycle management and preventive maintenance planning.
The combination of measurement data, visualization, evaluation by experienced employees, and anticipatory measures enables us to operate the production machines economically and avert events at an early stage.
Rudolf Raunig, head of infrastructure at INNIO Group in Jenbach
Valuable results
This technology-enabled, data-driven operations management project reduced INNIO Group’s overall environmental footprint. In fact, demand for electrical energy and compressed air on weekends was reduced by approximately 30% for the production machines included in the project, resulting in annual savings equivalent to the energy consumption of about 200 households.1
The energy measurement system also enhances condition monitoring. For instance, it detected a disconnected compressed air hose from a spindle unit and blown-out built-in air chokes. Based on these discoveries, prompt actions were taken to prevent the loss of compressed air, which represented a third of the full-load compressed air demand. In another instance, the system identified two separate air leaks – one that raised the baseline consumption and another that increased the peak consumption.
Spreading the word
Read the full 4E EMSA report here.
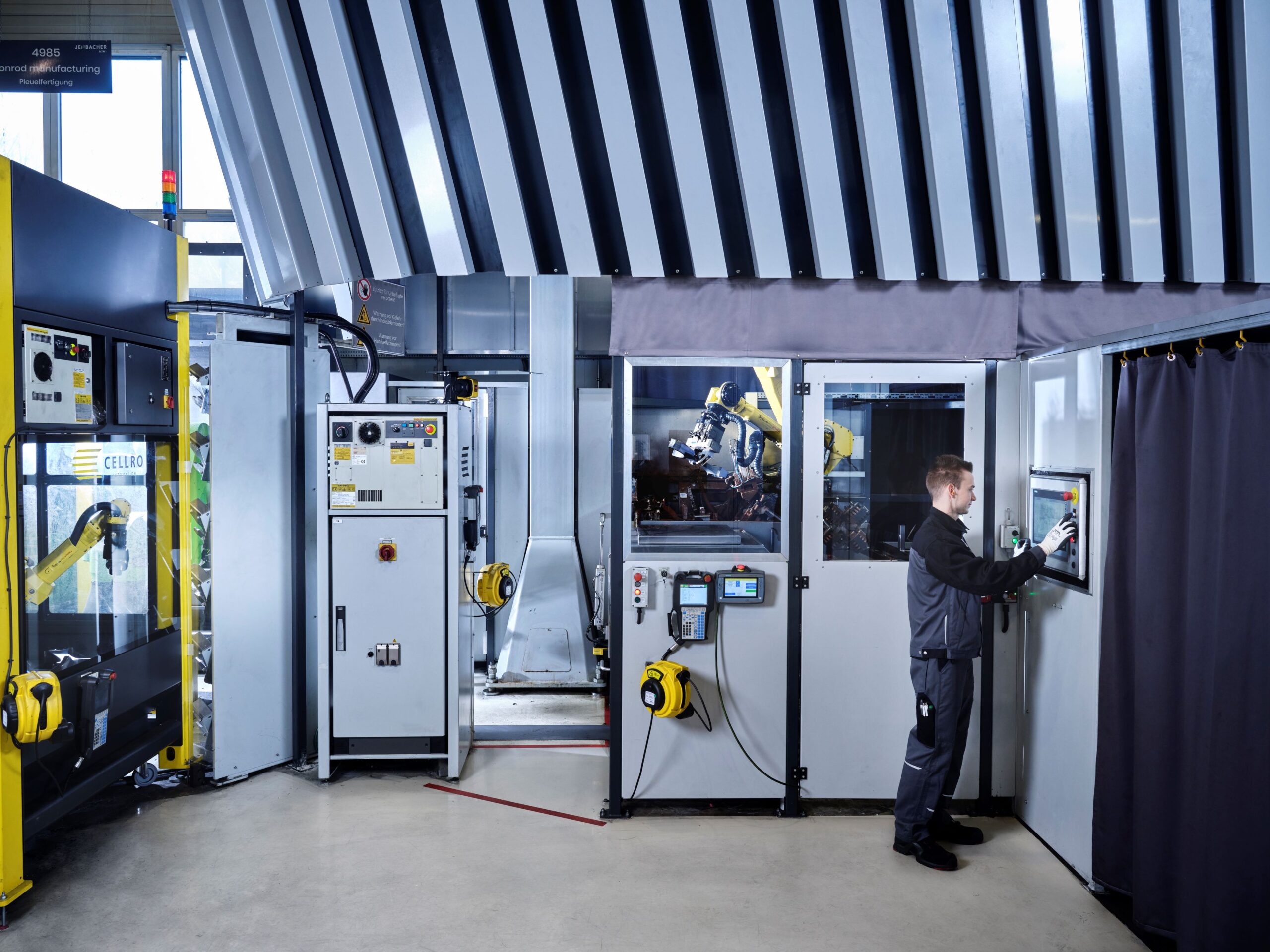
1 Basis for calculation: oesterreichsenergie.at