A first-of-its-kind solution from INNIO Waukesha Gas Engines Inc. and Detechtion Technologies Inc. can boost the performance of both natural gas engines and compressors through enhanced remote monitoring. The cloud-based digital solution provides a new depth of remote asset insights and analysis across a fleet of installed natural gas engine and compressor packages.
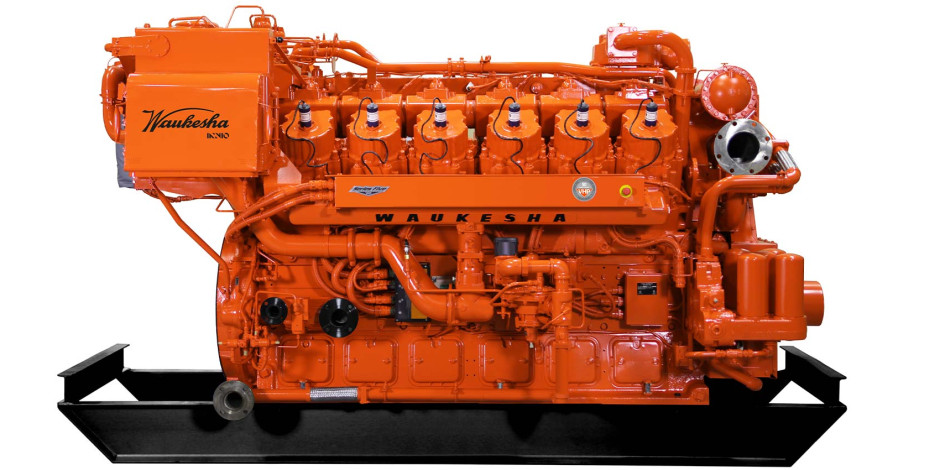
2022
monitoring begun
7
assets providing proof of concept
The technology partnership combines INNIO’s Waukesha engine analytics with Detechtion’s compression monitoring and optimization technology into a single digital solution for both new and existing compressor skids. The digital solution helps customers remotely manage their assets securely and in real-time, anticipating unexpected events and determining if assistance is required. The results: improved energy production and reduced plant downtime. For the collaboration, INNIO and Detechtion worked with a large international fleet rental company on a proof of concept. Seven assets—three in Bolivia and four in Oman—were selected by the customer. Once the systems were installed and running, the assets were monitored remotely by the Remote Operations Center (ROC) at the Waukesha site, which teamed up with the engineering account managers (EAMs) at Detechtion. The monitoring included ;
- Incremental production
- Fuel gas used
- CO2 and NOx emissions
- Expected discharge temperature
- Compression ratio
- Volumetric efficiency
- Blowby
- Rod load compression and tension—static and net
- Minimum degrees reversal
- Minimum rod load net ratio
- Cylinder flow
- Horsepower used—overall and at RPM
- Cylinder capacity used
Most systems today monitor the performance of either the compressor or the engine—never both. This comprehensive solution combines INNIO’s strength in engine analysis with Detechtion’s wide range of compressor diagnostics. Our collaboration strengthens our customer-centric strategy, helping drive the transition to net zero.
Bud Hittie, president of INNIO Waukesha Inc. and leader of the Waukesha product brand
When the ROC identified “blowby” on one of the assets, it quickly sent this information to an EAM for verification. If left untreated, blowby leakage on a compressor can be expensive and even catastrophic. The customer was proactively contacted by the ROC and EAM teams and was able to respond to the issue in a timely manner, reducing downtime and production losses.
Through the collaboration, the customer gained full visibility into the compressor package (engine and compressor), which often results in
- Lower operating costs
- Reduced asset downtime
- Increased asset availability
- Increased runtimes
- Increased production and/or lower emissions and fuel gas usage
- Decreased risk of catastrophic failure
- Reduced number of trips to field locations The collaboration will continue to remotely monitor the assets and proactively identify issues as they arise.
This collaboration will benefit the industry’s need for solutions that provide deeper visibility and better control throughout the compressor skid while optimizing operators’ operations. Both Detechtion’s and INNIO’s Waukesha teams have a wealth of knowledge and are energized to create an even more powerful solution that achieves the accessibility customers deserve. Detechtion has been creating digital twins and smart solutions to provide our compression customers with optimization and monitoring capabilities for over 20 years. We are excited to develop a combined solution alongside the Waukesha team.
Christopher Smith, president and CEO, Detechtion Technologies
Want to know how the proof of concept came about? Here are more details:
To ensure that the hardware would be plug and play once it arrived at site, various information was obtained from the customer ahead of time, including make/model, compressor geometry (such as bore, stroke, rod length, and rod load limits), engine geometry, and gas composition (fuel and compressed gas). After receiving installation training, the customer installed Detechtion’s Enbase Hubs—a process that averages 1 hour per device with remote support. Because the Oman site didn’t have all the necessary data requirements to enable the full functionality of Detechtion’s digital twin, an expansion module was quickly shipped to the site. The customer then was able to install pressure and temperature transducers without the need for costly controller reprogramming. The digital twins were built in Enalysis, the preferred predictive SaaS system Detechtion has developed for natural gas compressor fleet optimization. After the Hub communication was established and the data was confirmed to be valid, the Enbase Hub data began feeding into Enalysis to generate exception-based diagnostic reports.
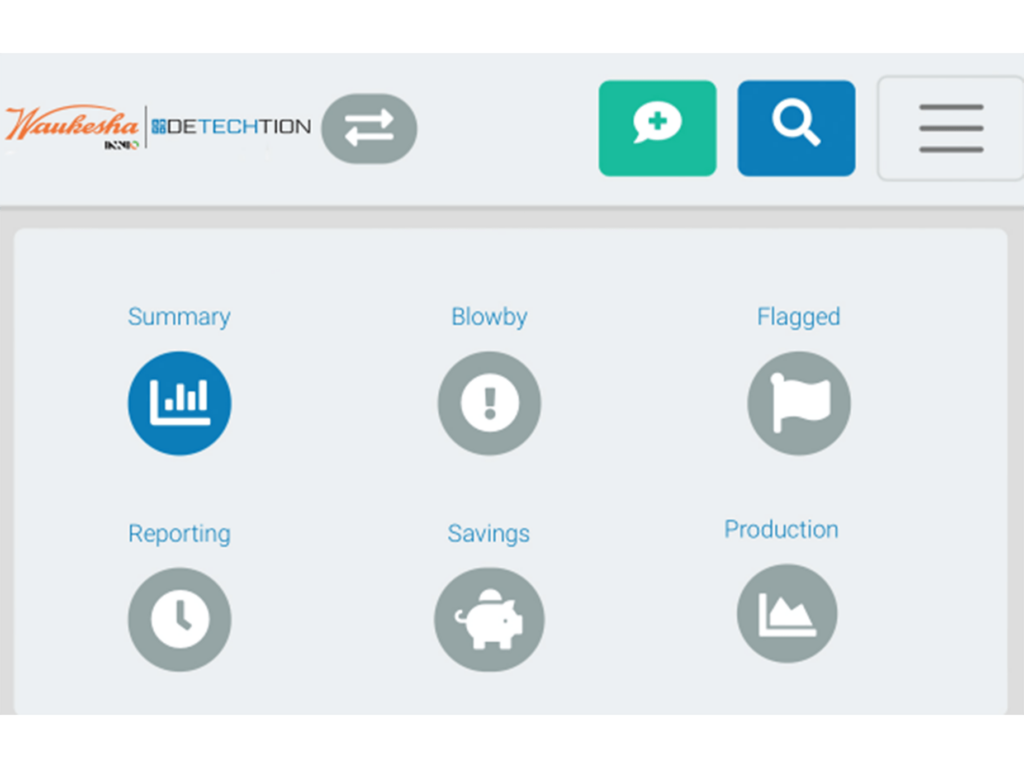
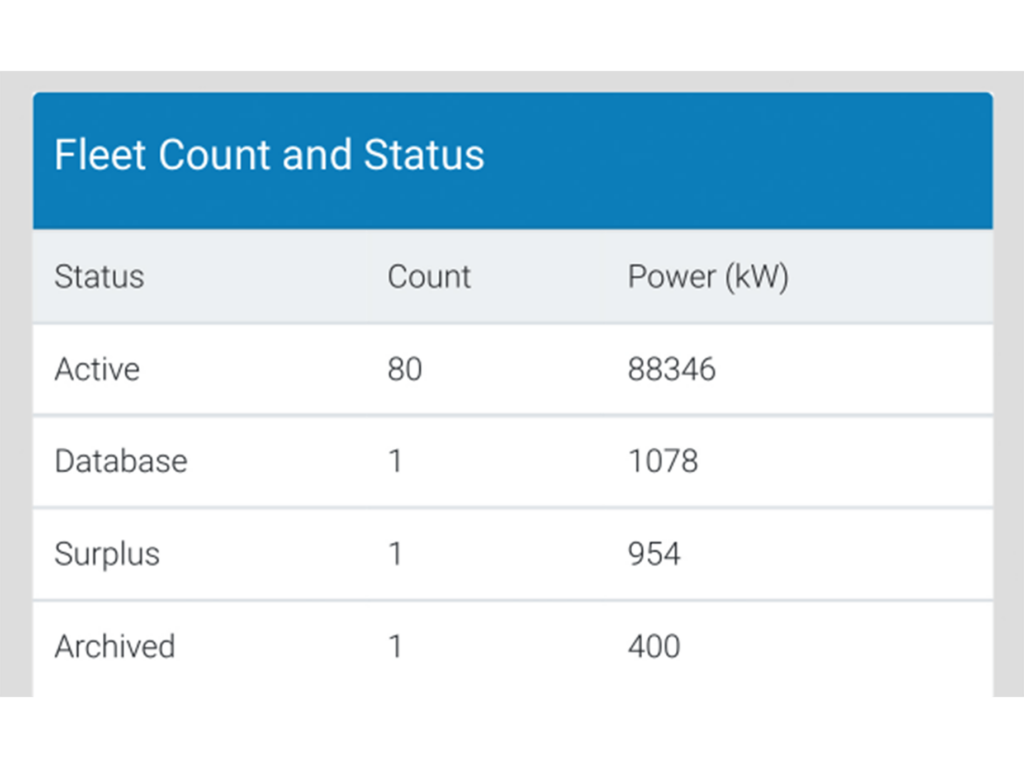
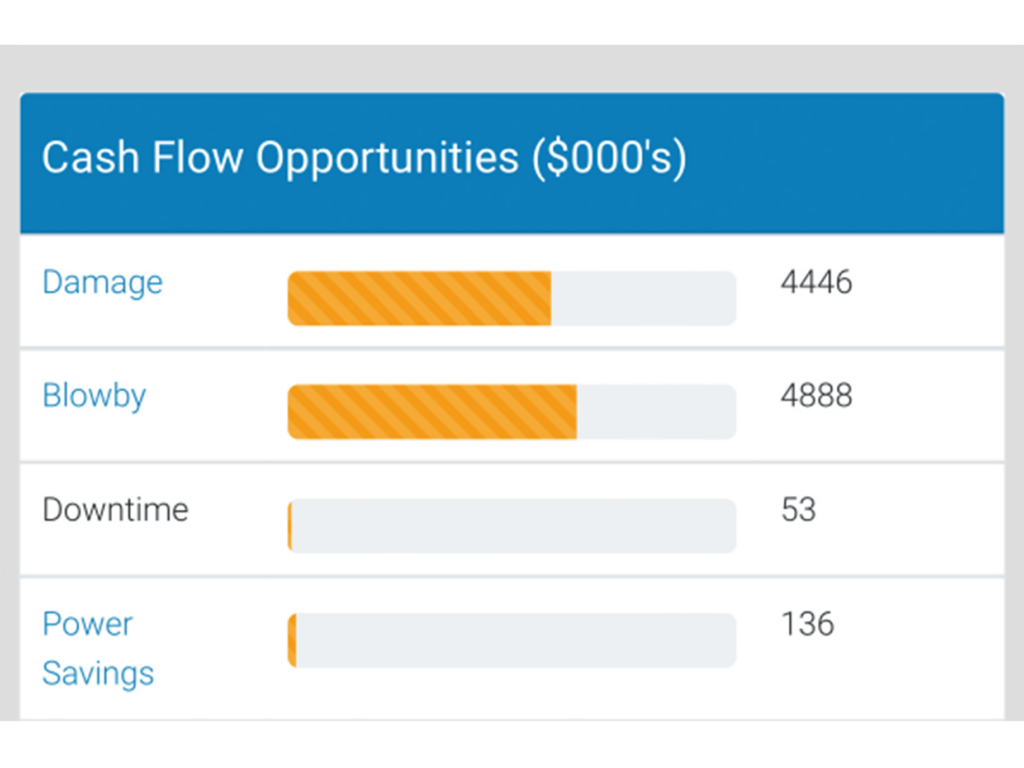
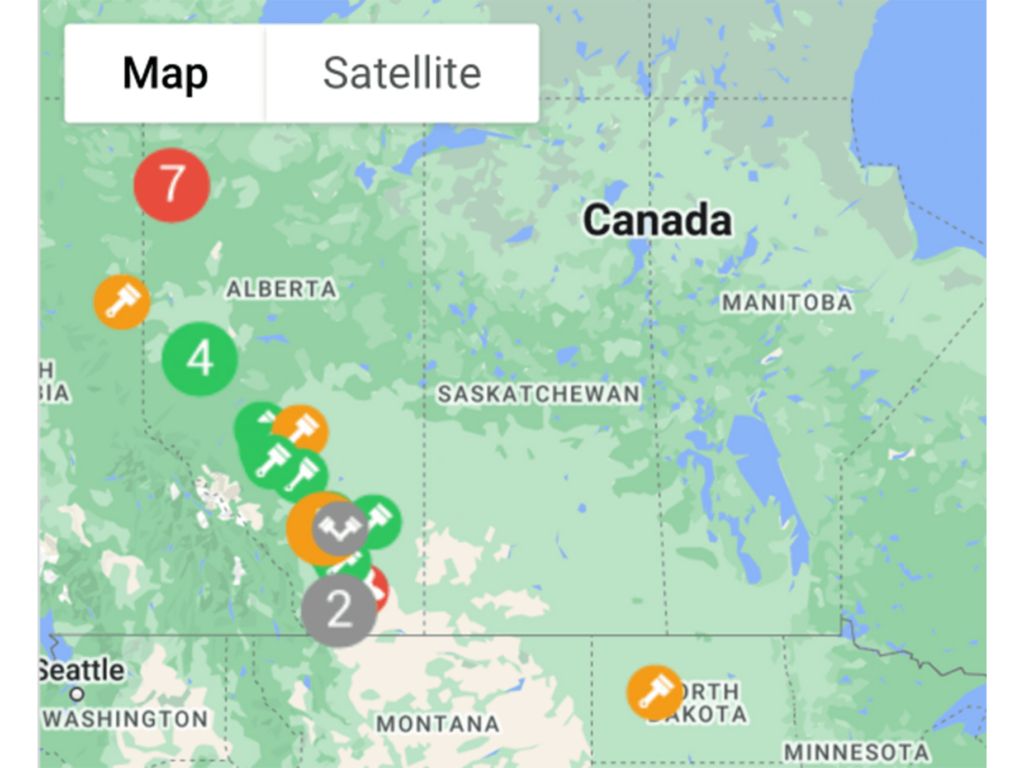
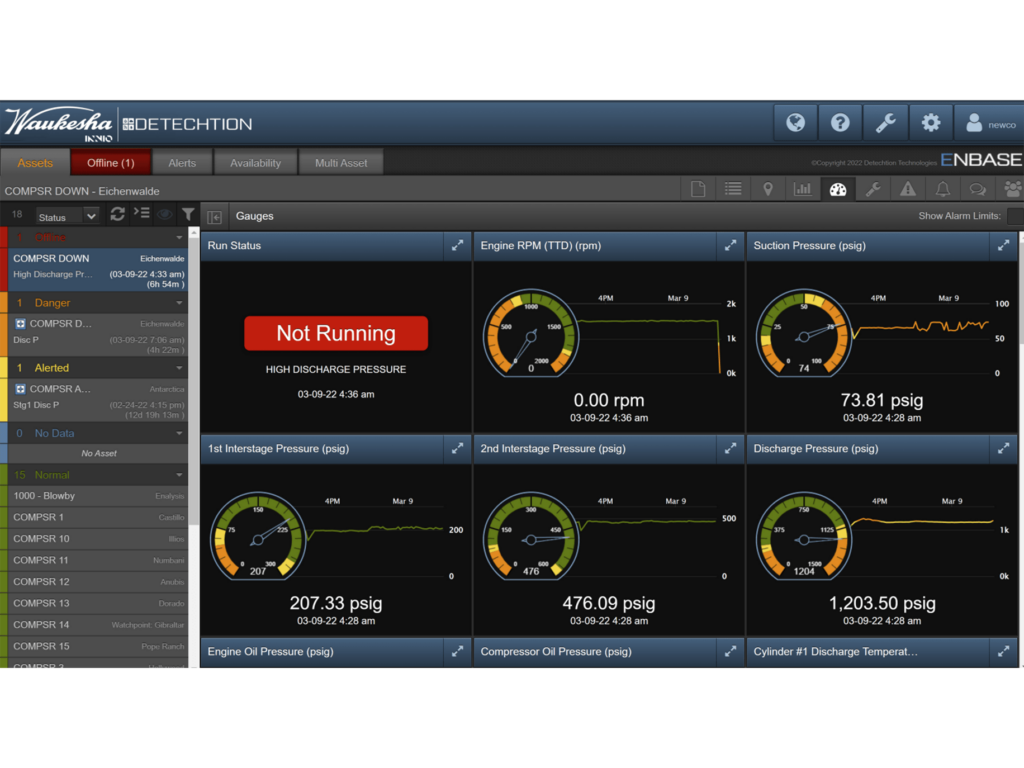